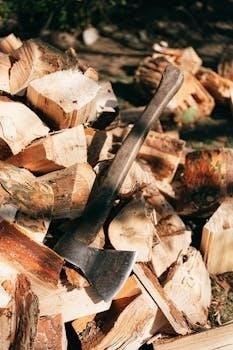
Manual Handling Risk Assessment⁚ An Overview
Manual handling risk assessments are essential for preventing musculoskeletal disorders (MSDs). These assessments identify hazardous manual handling tasks. They also define control measures to ensure tasks are completed safely. The process is applicable across various industries, enhancing workplace safety and compliance.
What is a Manual Handling Risk Assessment?
A manual handling risk assessment is a systematic evaluation of tasks involving lifting, carrying, pushing, or pulling. Its primary goal is to identify potential hazards and risks associated with these activities. The assessment aims to determine the likelihood and severity of injuries. It also aims to implement appropriate control measures to minimize these risks. These controls could include changing the process, introducing machinery, reorganizing the workplace, or training staff. Ultimately, the goal is to protect employees from musculoskeletal disorders and other related injuries.
Legal Requirements⁚ Manual Handling Operations Regulations 1992
The Manual Handling Operations Regulations 1992 mandate that employers must avoid, so far as is reasonably practicable, the need for employees to undertake manual handling operations at work which involve a risk of injury. Where avoidance isn’t possible, employers must conduct a suitable and sufficient risk assessment of all manual handling activities. This assessment should consider the load, task, individual’s capabilities, and the environment. The regulations also require employers to implement appropriate control measures. These measures should reduce the risk of injury to the lowest level reasonably practicable, ensuring a safe working environment.
Types of Manual Handling Risk Assessments
Manual handling risk assessments come in different forms. These include standard risk assessments. Dynamic risk assessments are also included. Each type addresses specific needs. They also cater to different operational scenarios within a workplace environment.
Standard Risk Assessments vs. Dynamic Risk Assessments
Standard risk assessments are proactive. They are conducted before new premises open. They are also carried out after a large intake of new staff. Dynamic risk assessments identify hazards as they appear. They are often due to tasks being carried out on the premises. Dynamic assessments are more frequent. They address immediate risks during ongoing operations, unlike standard assessments.
Dynamic Risk Assessment Example⁚ Recycling Plant Scenario
Consider workers in a recycling plant encountering an unknown object needing moving. Or, a construction worker needing to move a large item into a skip. In such cases, dynamic risk assessments are crucial. Workers must quickly define the hazards and risks involved. They must assess how to handle the object safely. This immediate evaluation is essential for preventing injuries during unexpected manual handling tasks.
Core Elements of a Manual Handling Risk Assessment
A comprehensive manual handling risk assessment covers four core elements. These elements are load, task, individual, and environment. Addressing each aspect ensures a thorough evaluation. It also mitigates potential risks effectively in manual handling operations.
Load Assessment⁚ Weight, Size, and Stability
When assessing a load, consider its weight, size, and stability. Heavy or unwieldy loads pose a greater risk of injury. Unstable loads can shift during handling, leading to accidents. Evaluate whether the load can be broken down into smaller, more manageable chunks. Determine if specialist machinery can be used to mitigate risks associated with the load’s characteristics. Proper load assessment is critical for ensuring safety during manual handling tasks and preventing injuries.
Task Assessment⁚ Movements, Repetition, and Distance
Task assessment involves analyzing movements, repetition, and distance. Unnatural movements like reaching or over-stretching increase risk. Repetitive tasks can lead to strain injuries. Long distances, generally over 10 meters, elevate the risk of manual handling. Evaluate the necessity of these movements and look for ways to reduce them. Proper task assessment helps identify and mitigate potential hazards. The goal is to streamline tasks to minimize physical strain and prevent injuries associated with these factors.
Individual Assessment⁚ Physical Capabilities and Training
Individual assessment determines who can safely perform manual handling tasks. Evaluate physical capabilities like strength and stamina. Ensure personnel have adequate manual handling training. Competent individuals are crucial for risk mitigation. Training equips workers to recognize hazards and use safe techniques. Assess whether individuals are physically suited for specific tasks. Proper training and physical suitability minimize injury risks. The goal is to match tasks to individuals with the right skills and physical condition, fostering a safer work environment.
Environment Assessment⁚ Space, Lighting, and Hazards
Environmental assessments focus on the surrounding workspace. Sufficient space is essential for safe movement. Adequate lighting reduces the risk of accidents. Identify and eliminate hazards in the work area. Clear obstacles to prevent trips and falls. Ensure the environment supports safe manual handling practices. Consider changeable circumstances, like weather. Address environmental factors that could increase risk. Well-managed environments contribute to safer operations. If needed, mechanical assistance might be required. Evaluating these components will minimize the risk factors.
The LITE/TILE Acronyms for Risk Assessment
LITE and TILE are acronyms simplifying manual handling risk assessments. These tools aid in remembering key assessment areas. LITE focuses on Load, Individual, Task, and Environment. TILE rearranges these elements. Using either acronym ensures comprehensive risk evaluation.
LITE⁚ Load, Individual, Task, Environment
The LITE acronym provides a structured approach to manual handling risk assessments, ensuring all critical factors are considered. “Load” involves assessing weight, size, and stability. “Individual” considers physical capabilities and training. “Task” examines movements, repetition, and distances. “Environment” focuses on space, lighting, and potential hazards. By evaluating each element—Load, Individual, Task, and Environment—organizations can identify risks and implement appropriate control measures, promoting a safer working environment. This systematic approach helps prevent injuries associated with manual handling operations. Properly addressing each component minimizes potential harm, ensuring employee well-being and regulatory compliance.
TILE⁚ Task, Individual, Load, Environment
TILE, an alternative acronym, rearranges the assessment focus, beginning with “Task,” evaluating movements and repetition. Next, “Individual” assesses physical capabilities and training. “Load” considers weight, size, and stability. Finally, “Environment” examines space, lighting, and hazards. Like LITE, TILE ensures comprehensive risk assessment. TILE prioritizes the specific actions required, followed by the person performing them, then the object handled, and lastly, the surroundings. This approach ensures risks are mitigated effectively. Organizations can adopt either LITE or TILE based on their operational needs, improving safety and reducing the risk of manual handling injuries.
Steps in Performing a Manual Handling Risk Assessment
Performing a manual handling risk assessment involves avoidance, assessment, and review. Avoidance aims to eliminate the task if possible. Assessment includes workforce involvement. Review ensures smooth implementation and continuous improvement. These steps reduce manual handling incidents effectively.
Avoidance⁚ Can the Task Be Eliminated?
The initial step in a manual handling risk assessment is avoidance. Can the manual handling task be eliminated entirely? Employers should, as far as reasonably practicable, avoid the need for employees to undertake manual handling operations that involve a risk of injury. Consider using machinery or redesigning the process. Avoiding hazardous manual handling is crucial, especially considering potential compensation claims for work-related injuries, which can be substantial. Prioritizing avoidance minimizes risks and promotes a safer working environment for all employees involved.
Assessment⁚ Involving the Workforce
If avoidance isn’t possible, proceed with a comprehensive assessment. Involve the workforce in this process for complete coherence. Ascertain how manageable the task is, considering key elements such as movements, repetition, and distances. Identify risk factors and potential improvements collaboratively. Employee input is crucial for identifying hidden hazards and ensuring the assessment reflects real-world conditions. This collaborative approach fosters a safer work environment and promotes ownership of the risk management process. A thorough assessment helps reduce manual handling incidents effectively.
Review⁚ Ensuring Smooth Implementation
Following any assessment, a review is essential to ensure smooth implementation and address complications. A Team Leader or Line Manager should conduct the review to ensure correct implementation going forward. This stage irons out any issues for future assessments. Regular reviews maintain the effectiveness of control measures. Reviewing the process ensures that the risk assessment remains relevant and up-to-date. Adaptations can be made based on workforce feedback and operational changes. This continuous improvement cycle enhances safety and reduces manual handling incidents, promoting a healthier work environment.
Competent Person Requirement
A competent person must conduct manual handling risk assessments. The Health and Safety Executive (HSE) emphasizes that competent personnel should be sufficiently trained. Completing manual handling training ensures the assessor has the required skills and knowledge.
Defining a Competent Person⁚ Training Requirements
Defining a competent person is crucial for effective risk management. A competent person must possess adequate training and experience; This ensures they can accurately identify and assess manual handling risks. Proper training equips individuals with the knowledge to implement appropriate control measures. Such measures mitigate the risk of injuries. Health and Safety Executive (HSE) guidelines emphasize the necessity of qualified personnel. This qualification guarantees thorough and reliable risk assessments in the workplace, promoting a safer environment for all employees.
Control Measures and Risk Mitigation
Control measures and risk mitigation are crucial. They reduce manual handling incidents. Implementing a hierarchy of control methodology is essential. Using machinery and equipment also helps. This minimizes risks associated with manual handling tasks.
Hierarchy of Control Methodology
A manual lifting risk assessment generally follows a hierarchy of control methodology for mitigating risk. This approach prioritizes eliminating hazards first. If elimination isn’t possible, then risk reduction strategies are implemented. These strategies include substituting hazardous tasks with safer alternatives. Engineering controls, such as mechanical aids, are considered next. Administrative controls, like training and procedures, follow. Finally, personal protective equipment (PPE) is used as a last resort. This systematic approach ensures effective risk reduction and worker safety.
Using Machinery and Equipment to Reduce Risk
Incorporating machinery and equipment significantly reduces manual handling risks. Utilizing tools like forklifts, pallet jacks, and conveyors minimizes physical strain. Mechanical aids assist in lifting, carrying, and moving heavy loads. This reduces the risk of musculoskeletal injuries and fatigue. Selecting appropriate equipment depends on the task, load, and environment. Regular maintenance and training are crucial for safe equipment operation. Proper use of machinery enhances efficiency and protects workers. It also supports compliance with safety regulations. Prioritizing equipment use improves overall workplace safety.
Review and Updates
Regularly review and update the risk assessment to ensure control measures remain effective and relevant. Updates are necessary after workplace changes, like new equipment or processes. This maintains the assessment’s accuracy and improves safety protocols.
Regularly Review and Update the Risk Assessment
Periodic review and updates are crucial for maintaining the effectiveness of manual handling risk assessments. This process should be conducted regularly or whenever significant changes occur in the workplace. This includes new equipment, altered processes, or personnel changes. Ensuring control measures remain relevant and effective is essential. This proactive approach helps in continuously mitigating risks associated with manual handling tasks. Proper documentation of reviews and updates provides an audit trail for compliance and continuous improvement in safety practices.
Significant Changes in the Workplace
Whenever significant changes occur in the workplace, a review and update of the manual handling risk assessment is essential. These changes may include the introduction of new equipment, alterations in work processes, or modifications to the layout of the workspace. Personnel changes, such as new hires or changes in job roles, also necessitate a reassessment. The goal is to ensure that the risk assessment remains relevant and effective in light of the updated conditions. Any new hazards identified during the review should be promptly addressed.
Examples of Manual Handling Risk Assessments
Manual handling risk assessments vary across different work environments. Examples include offices, where assessments address ergonomics and lifting techniques. In manufacturing, assessments focus on heavy lifting and repetitive tasks. These tailored assessments ensure relevant risk mitigation.
Office Environment
In an office setting, manual handling risk assessments address tasks like lifting boxes of documents or equipment. Key considerations include workstation ergonomics and posture. Assess the placement of equipment and ensure proper lifting techniques are employed. Risks might involve awkward reaching, repetitive movements, and prolonged sitting. Implement measures such as adjustable chairs, proper training on lifting, and regular breaks. The goal is to prevent strains and musculoskeletal issues associated with office-related manual handling. Regular reviews should adapt to changes in office layout or tasks.
Manufacturing Sector
In manufacturing, manual handling risk assessments are critical due to heavy lifting and repetitive tasks. Assess the movement of raw materials, components, and finished products. Identify risks like heavy loads, awkward postures, and repetitive motions. Implement engineering controls such as conveyor systems and lifting aids. Provide training on proper lifting techniques and the use of equipment. Regular assessments must account for changes in production processes or materials handled. Mitigation strategies should focus on reducing strain and preventing musculoskeletal injuries among workers in this sector. Proper planning is essential.